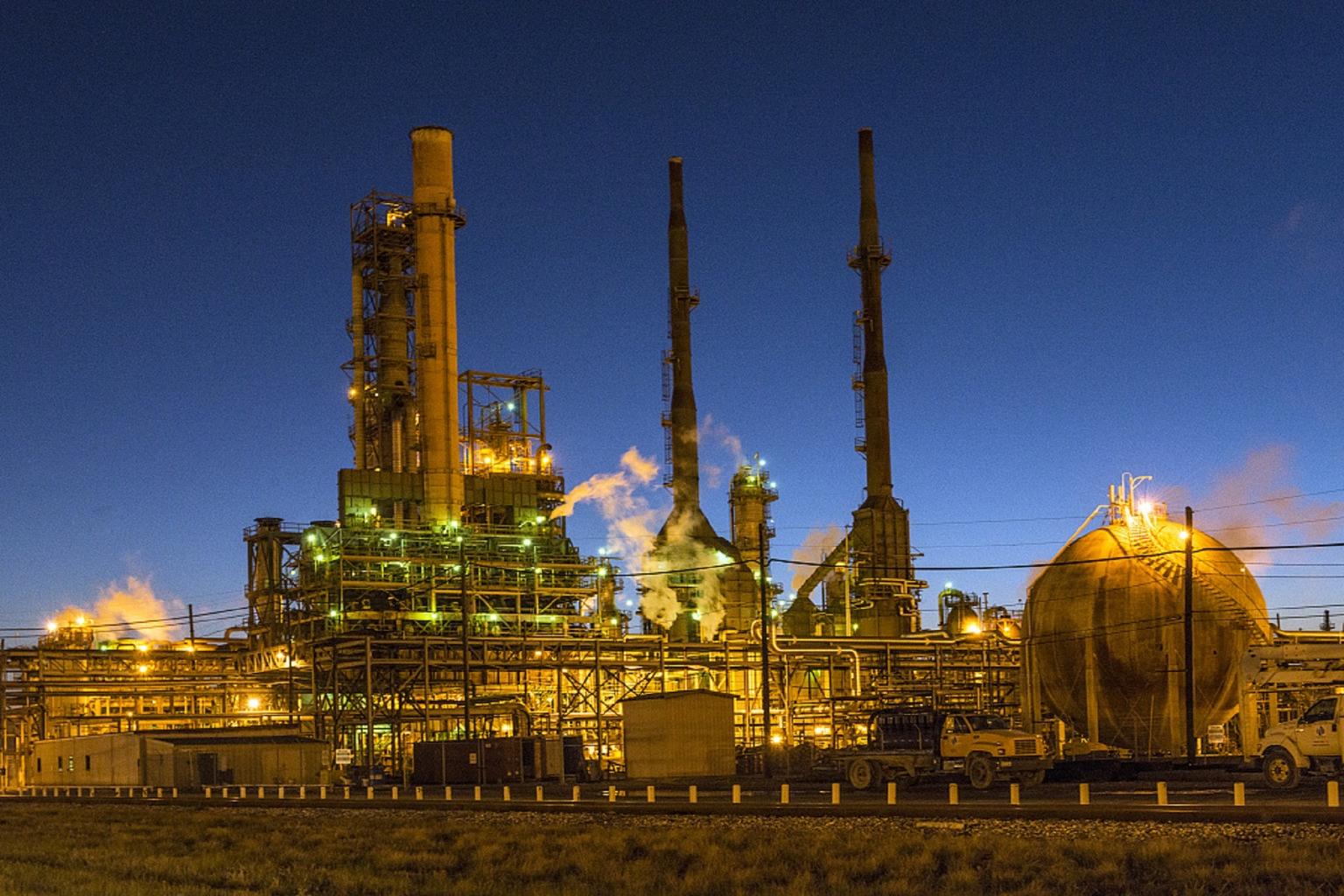
General Specifications of Explosive Environment and
MIL-STD-810 Method 51
What does Explosion Proof Really Mean:
To understand explosion proof, you need to look at the context of the term and the organization that defined it. The National Fire Protection Association (NFPA) began publishing the National Electric Code (NEC®) in 1897. The NEC® is also known as NFPA 70 and ANSI/NFPA 70 from its inclusion in the body of NFPA codes.
The NEC® includes definitions for several types of protection techniques acceptable when designing products for use in hazardous (classified) locations: Explosion proof, dust ignition proof, dust tight, purged/pressurized, intrinsically safe, and hermetically sealed. These definitions set the criteria that must be met by all components installed or used in hazardous (classified) locations.
To meet the criteria for the explosion proof rating, an enclosure must be able to contain any explosion originating within its housing and prevent sparks from within its housing from igniting vapors, gases, dust, or fibers in the air surrounding it. Therefore, explosion proof, when referring to electrical enclosures, does not mean that it is able to withstand an exterior explosion. Instead, it is the enclosures ability to prevent an internal spark or explosion from causing a much larger blast.
Additionally, the NEC states that equipment must meet the temperature requirements of the specific application in which it is to be installed or used. This means that the operating temperature of the device cannot be greater than the lowest ignition/combustion temperature of the gases or dusts in the atmosphere where it is being used. References.
WHAT IS A HAZARDOUS ENVIRONMENT?
Any location where explosions or fire may exists due to the presence of flammable liquids, gases, vapors, dust, or fibers. This is a general listing, but in all honesty no one can truly identify all of the locations that can be hazardous or generate guidelines that would work for every possible location or situation out there.
In order for materials to combust, a combustible substance must be around both oxygen, and something that creates a spark or a source of ignition. This can include gasoline, paint thinner, decomposing materials, or naturally occurring gases. With regards to the videoscopes that we offer, all of these units are currently classified for use in Class I Division 2 hazardous environments, as defined in the National Fire Protection Association Code (NFPA 70), Article 500, and tested using MIL-STD-810G, Method 511.6, Procedure I. We do not currently know of any videoscopes that are classified for Class I Division 1 use, or that are intrinsically safe. We are working on this certification process for oure Borescope – Videoscope XT Series, though.
Before using these products, you must know or be able to confirm the classification level of the hazardous location you will be working in, or inspection, to make sure that the proper criteria is met.
HOW DOES THE CLASSIFICATION SYSTEM WORK?
Within North America, hazardous locations are defined using a combination of classes and divisions as follows.
Classes
- Class I – A location made hazardous by the presence of flammable gases or vapours that may be present in the air in quantities sufficient to produce an explosive or ignitable mixture
- Class II – A location made hazardous by the presence of combustible or electrically conductive dust
- Class III – A location made hazardous by the presence of easily ignitable fibers or flyings in the air, but not likely to be in suspension in quantities sufficient to produce ignitable mixtures
Divisions
- Division 1 – A location where a classified hazard exists or is likely to exist under normal conditions
- Division 2 – A location where a classified hazard does not normally exist but is possible to appear under abnormal conditions
The U.S. and Canada have recently revised codes to recognize an international 3-Zone classification system for equipment used in hazardous locations. These are and will continue to come into effect moving forward.
- Zone 0 – An area in which an explosive gas atmosphere is continuously present for a long period of time
- Zone 1 – An area in which an explosive atmosphere is likely to occur in normal operation
- Zone 2 – An area in which an explosive gas atmosphere does not normally exist
The zone classification system these can be defined by hours as well, with Zone 0 having an ignitable concentration of flammable gases, vapors, or liquids present continuously or for long periods of time under normal operating conditions defined as over 1000 hours/year, Zone 1 defined as 10-1000 hours/year, and Zone 2 defined as ignitable concentrations of flammable gases, vapors, or liquids only present for under 10 hours/year (references).
HOW ARE THESE PROTECTION TECHNIQUES RATED?
Each of the protection techniques mentioned above is permitted for use only in very specific applications. For example, components and equipment complying to dust tight specification are approved for use in Class II, Division 2, or Class III, Division 1 or 2 locations, while those listed as explosion proof are approved for use in Class I, Division 1 or 2 locations.
Often, those products listed at a higher classification level surpass the requirements for lower classifications. The NEC® explicitly states “Equipment that has been identified for a Division 1 location shall be permitted in a Division 2 location of the same class, group, and temperature class,” thereby complying with requirements for the Division 2 areas [ANSI/NFPA 70:500.8(A)(2). References.
WHAT IS MIL-STD-801G METHOD 511?
This standard is a United States Military Standard to test equipment limits in various environmental conditions where it is expected to be used, or transported. It describes in detail testing procedures designed to determine how equipment holds up under a variety of conditions the equipment may encounter while being used, transported and stored. These conditions include temperature, impact (shock), vibration, humidity, explosive atmosphere, and more. This method is performed to demonstrate the ability of the material to operate in explosive atmospheres without causing ignition, or to demonstrate that an explosive or burning reaction occurring within encased material will be contained, and will not propagate outside the test unit.
Method 511 deals with 2 procedures, Procedure I where the unit operates in an explosive atmosphere without igniting the air/fuel mixture environment, and Procedure II which determines the ability of the test unit to contain an explosion or flame that is the result of an internal malfunction. Procedure II specifically relates to atmospheres in a space in which flammable fluids or vapors exist, or can exist, either continuously or intermittently. These tests involve placing the item inside a chamber filled with an explosive mixture, and keeping this at the maximum temperature the item may experience. For Procedure I, operate the unit in this explosive atmosphere to determine if it will ignite the mixture.
It is worth noting that during testing in vapors, the altitude changes, as does the ambient temperature – this is what makes it significantly more dynamic than the straight forward UL tests – the change in altitude and temperature create positive pressure and a vacuum environment in an attempt to “draw” vapors into the unit.
West Coast Explosion Proof Borescopes –
High Resolution Videoscopes The XT Series
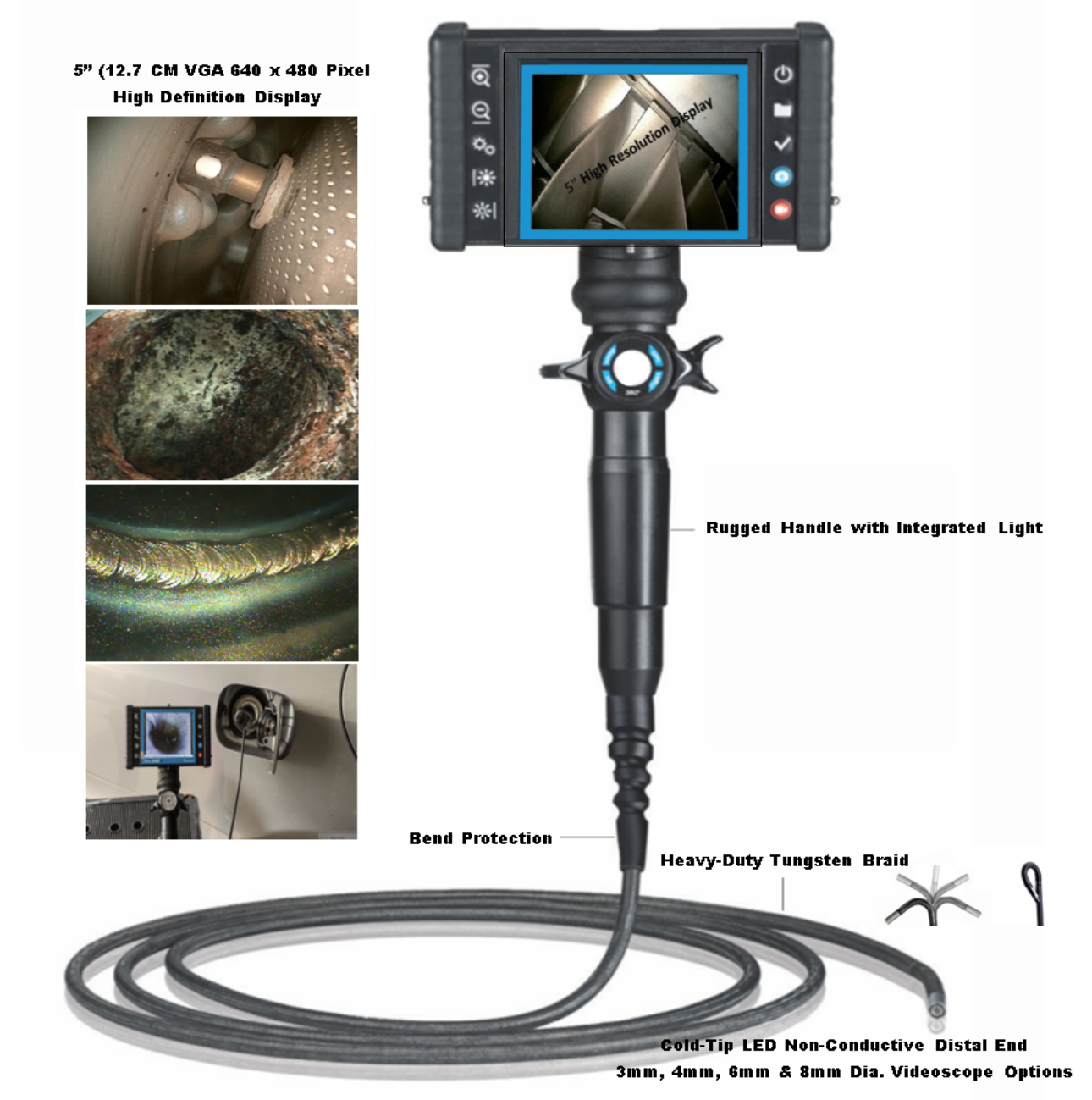
What is an Explosion Proof Borescope – Videoscope – ITSVideoscopes
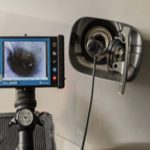
In order for an Explosion Proof Boresscope to meet the criteria for the Explosion Proof Rating, its enclosure must be able to contain any explosion originating within its housing and prevent sparks from within its housing from igniting vapors, gases, dust, or fibers in the air surrounding it. Therefore, explosion proof, when referring to electrical enclosures, does not mean that it https://www.itsvideoscopes.com/borescopes-explosive-volatile-environment-its-videoscopes-xt-plus-series/is able to withstand an exterior explosion. Instead, it is the enclosures ability to prevent an internal spark or explosion from causing a much larger blast.
What does Explosion Proof Mean
To understand explosion proof, you need to look at the context of the term and the organization that defined it. The National Fire Protection Association (NFPA) began publishing the National Electric Code (NEC®) in 1897. The NEC® is also known as NFPA 70 and ANSI/NFPA 70 from its inclusion in the body of NFPA codes.
The NEC® includes definitions for several types of protection techniques acceptable when designing products for use in hazardous (classified) locations: Explosion proof, dust ignition proof, dust tight, purged/pressurized, intrinsically safe, and hermetically sealed. These definitions set the criteria that must be met by all components installed or used in hazardous (classified) locations.
WHAT IS A HAZARDOUS ENVIRONMENT?
Any location where explosions or fire may exists due to the presence of flammable liquids, gases, vapors, dust, or fibers. This is a general listing, but in all honesty no one can truly identify all of the locations that can be hazardous or generate guidelines that would work for every possible location or situation out there.
WHAT IS MIL-STD-801G METHOD 511?
This standard is a United States Military Standard to test equipment limits in various environmental conditions where it is expected to be used, or transported. It describes in detail testing procedures designed to determine how equipment holds up under a variety of conditions the equipment may encounter while being used, transported and stored. These conditions include temperature, impact (shock), vibration, humidity, explosive atmosphere, and more. This method is performed to demonstrate the ability of the material to operate in explosive atmospheres without causing ignition, or to demonstrate that an explosive or burning reaction occurring within encased material will be contained, and will not propagate outside the test unit.